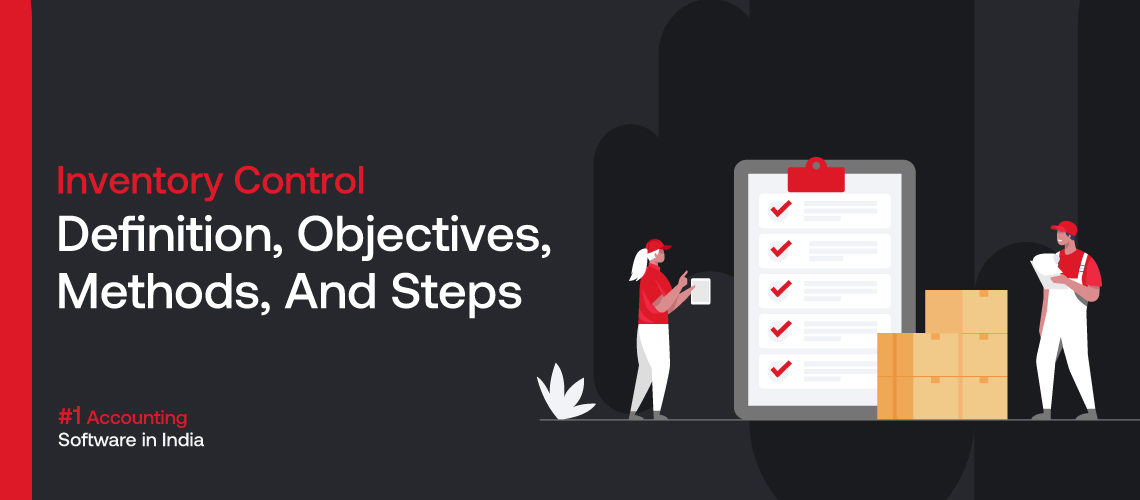
Inventory control is necessary for businesses since it affects revenue and client retention. It requires overseeing inventory from the time it enters the warehouse until it is sent, maintaining ongoing physical accessibility, and using various strategies to keep the inventory quality high. To maximize stock, eliminate non-sellers, and expedite procurement, inventory control systems can be deployed utilizing a variety of software, including barcodes and SKUs. With the help of this blog, businesses may optimize their inventory and increase sales by understanding inventory control objectives and how to put them into practice.
Defining Inventory Control
Inventory control techniques like the two-bin system, quality control, barcode scanning, and forecasting are used to reduce stock in warehouses and promptly fill client orders. It considers factors including lead times for individual commodities, perishables' shelf lives, seasonal inventory items, consumer demand, and available storage space. Accounting and inventory management software ensures businesses have enough stock to fulfill anticipated needs while incurring the fewest holding expenses.
Objectives Of Inventory Control
Optimizing Cost
Inventory management attempts to reduce the cost of purchasing and maintaining inventory while maintaining appropriate costs and high customer satisfaction. This involves lowering the cost of placing orders and maintaining inventory during production to maintain low overall selling costs.
Increasing Profit
Poor inventory control negatively influences earnings by minimizing stock wastage and making it challenging to pick products out of warehouses. Customers may suffer as a result of orders not being fulfilled on time. Effective inventory control has a favorable impact on revenue by reducing lost money in expired goods and eliminating inefficiencies during stock movements between storage facilities.
Securing The Availability Of The Product
Inventory control is essential for warehouses to operate efficiently, especially in industrial businesses. It seeks to ensure prompt order fulfillment by sustaining an uninterrupted supply of raw materials and subassemblies. This is particularly important for distribution companies, where goods are selected and packaged for transportation. Disorganized warehouse layouts and far-off products can also cause bottlenecks.
Reducing Wastage
Either the stock is flawed, or the stock has expired, which leads to inventory waste. Additionally, it occurs when there is no market demand, and the stock sits idle. Here, inventory control tries to avoid dead stock or an accumulation of expired items and the entry of defective stock into your warehouses through quality control.
Creating Space
Space is needed for inventory storage. Actively managing your inventory, warehouse layouts, and locations reduces the need for additional storage space, which lowers your rental expenses. Additionally, it entails getting rid of surplus, dead, and expired stock. You'll save storage space for the goods that sell better if your storage rooms are well-planned and not filled with dead stock.
Steps To Follow In Inventory Control
Step 1. Decide Levels Of Inventory
The effectiveness of a manufacturing department depends on how well it works with sales and marketing. Determining inventory levels and maximum-minimum restrictions is essential because sales and marketing evaluate customer demand and product requirements. Manufacturers should refrain from stocking limited-use materials or obsoleting raw resources to manufacture final goods.
Step 2. Determine Production And Stock Levels
Demand for goods is unpredictable in today's uncertain world, particularly given consumer preferences and interests. Manufacturers must choose the manufacturing volume and replenish raw materials for the finished product to satisfy client requests. Delivery delays result from the inability to deliver the product to the consumer if restocking takes longer.
Step 3. Choose The Appropriate Inventory Control Method
Businesses can use a variety of inventory control techniques, but it's important to pick one that aids in determining the minimum stock level, reorder point, and appropriate order quantity. Techniques should make it easier to keep the inventory level constant.
Inventory Control Methods
Economic Order Quantity
EOQ is a formula for determining the ideal inventory quantity for a company, considering factors like production costs and demand. It frees up tied cash and reduces direct costs. Inventory accounting software can improve inventory management.
ABC Analysis
The inventory management system categorizes inventory into three buckets: A, B, and C, based on its importance to profit. A category has expensive items, while B has average-priced inventory with medium sales frequency. Category C has low value but high sales frequency, requiring less inventory control than A or B.
Just-In-Time Inventory Management
Arranging raw material orders in sync with production schedules reduces inventory costs by preventing excess storage beyond production requirements, minimizing deadstock in the organization.
Safety Stock Inventory
Businesses might order more inventory than they anticipate being needed as buffer stock. It corrects the underestimation of demand.
FSN: Fast, Slow, And Non-Moving
To determine how quickly a business can place orders, inventories are divided into fast-moving, slow-moving, and non-moving goods.
Conclusion
Inventory is money that is kept in a different form and returned when sold. To manage inventory effectively, Indian businesses today employ the best inventory management software in india with automated management methods. This software lets firms quickly decide based on consumption by calculating net stock, shortage, and stock quantity.